フリアーシステムズのコンパクトなサーマルイメージ放射温度計により、パッケージ品質を常時監視
見た目と配送方法も、製品品質の重要な一翼を担っています。 化学製品・液体を取り扱っているカナダのメーカー(サプライヤー)、Recochem社は、このことを熟知しています。 そのため、同社はサーモグラフィカメラを導入し、パッケージのシーリング品質を継続的に監視しています。
Recochem社はカナダの民間企業で、高品質な製品と優れた顧客サービスを提供していることで広く知られています。 同社の南北アメリカ事業部は、住宅関連の化学製品や自動車用の液類の製造・調合・包装・梱包・卸売業務を請け負っており、カナダ国内に5つの拠点を構えています。
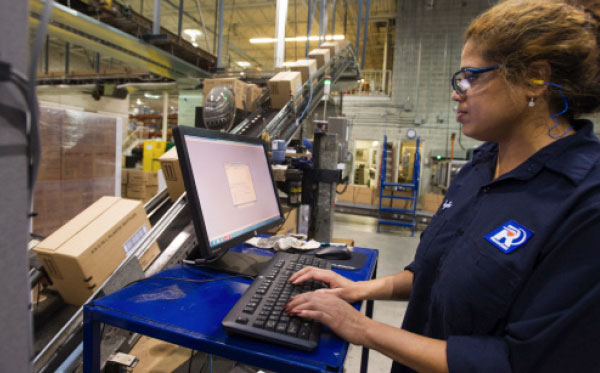
パッケージ品質と製品品質
Recochem社のプラントエンジニアリング責任者、Adam Wolszczan氏は、次のように述べています。「パッケージは、製品の品質と安全性を確保する上で、極めて重要です。 当社のウォッシャー液は、容器に入った状態で届きますが、これを段ボール箱に梱包します。 製品を包んで保護する箱の品質は、常に一定に保つ必要があります。」
箱に封をする際、最も費用効果の高い方法の一つは、箱のフラップ部にホットメルト接着剤を塗布する方法です。 しかし、現場のプロセスにおいては、接着剤の塗布が不正確だったり、不十分だったりする場合もあります。 そのためRecochem社では、接着剤が実際に塗布されたか、また適切な位置に塗られたかを検査するためのソリューションを求めていました。
品質検査
「従来は、品質を調べるため、一定周期ごとに箱を生産ラインから取り出し、箱を壊して検査を行っていました」と、Adam Wolszczan氏は語ります。 「この作業にはとても時間がかかるだけでなく、大幅なコスト増にもつながっていました。」
Recochem社は、効率的な接着剤モニタリング手法を求めて、まずはシングルスポットの赤外線センサーを試してみることにしました。 「接着剤は熱を帯びているため、その温度情報から塗布状況を検査できると考えました」と、Adam Wolszczan氏は語ります。 「しかし、箱の底部のフラップを検査できる位置に赤外線センサーを設置することはできませんでした。 また、フラップが開いている状態でなければ、赤外線センサーで塗布状況を調べることもできませんでした。」
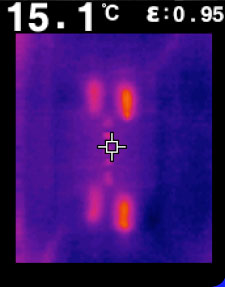
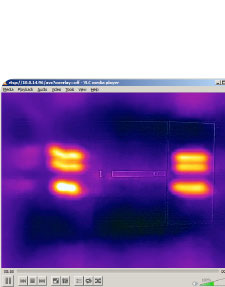
段ボールを見通すサーモグラフィ
効果的なモニタリング方法の導入を検討するというRecochem社のミッションは、サーモグラフィと出会ったことでようやく前進しました。 Adam Wolszczan氏は、次のように述べています。「私は、サーモグラフィという技術があることは以前から知っていました。 会社では、屋根のメンテナンスや電気パネルの検査などを業者に委託していたので、湿度の状況や断熱材の脱落などについて調べるためにサーモグラフィが有効であることは分かっていました。 そこで、私はサーマルイメージ放射温度計FLIR TG165を購入し、梱包プロセスの監視に応用できるか検討してみました。 その結果はバッチリでした。」
Adam Wolszczan氏は、生産ラインから箱をいくつか取り出し、TG165で調べてみたところ、カメラには接着剤のホットスポットがはっきりと映り込んでいました。 さらに、サーマルイメージ放射温度計FLIR TG165は、段ボールを見通し、塗られているホットメルト接着剤のパターンやサイズもチェックすることができます。 つまり、箱をわざわざ壊して検査を行う必要がなくなります。 そのためAdam Wolszczan氏は、サーモグラフィを正式に導入することを決めました。「フリアーシステムズに問い合わせて、温度センサーFLIR AX8というぴったりのソリューションを見つけてもらいました。 AX8はお手頃で、非常にコンパクトです。当社の用途に最適でした。」
コンパクトで設置も簡単
導入されたAX8カメラは、現在では、フラップ上の接着剤が塗られる位置を撮影するよう設定され、該当スポットのサイズや温度を確認するために使われています。 温度センサーAX8はコンパクトなため、箱の底部を撮影できる位置に設置することも可能です。 また、段ボールを通過する熱も捉えることができるため、検査用に箱を壊す必要もなくなりました。 撮影された映像は、オペレーターが専用画面で確認できます。
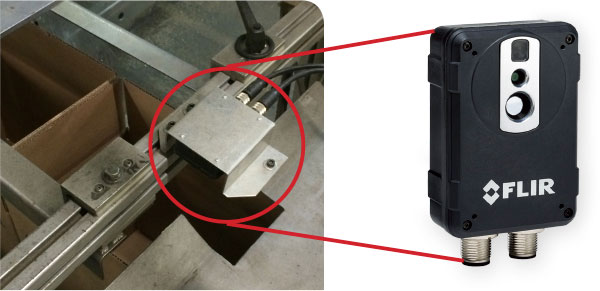
「AX8で撮影された赤外線画像を見ると、接着剤が塗られて熱くなっている箇所(ホットスポット)をはっきり確認できます。 グルーガンの動作が遅れると、ホットスポットの位置がずれるため、何らかの問題が起きていることが即座に分かります。 とても簡単で効果的です。」
製品品質の向上
「サーモグラフィの大きなメリットとして、品質の問題を以前よりもはるかに迅速かつ効率的に発見できるようになりました」と、Adam Wolszczan氏は語ります。 「赤外線画像は、オペレーターにとって非常に便利ですが、シングルスポットの赤外線センサーでは、塗布状況の合否しか判定できず、詳しい情報が分かりません。」
「おかげさまで、より良い製品をお客様に提供できるようになっただけでなく、作業時間の大幅な短縮も可能になりました。 以前は、オペレーターが10~15分ごとに箱を壊して検査を行う必要がありました。当社の生産ラインは週に5日間、ほぼ1年中稼働しているため、作業時間とコストの削減は非常に大きなテーマです。」